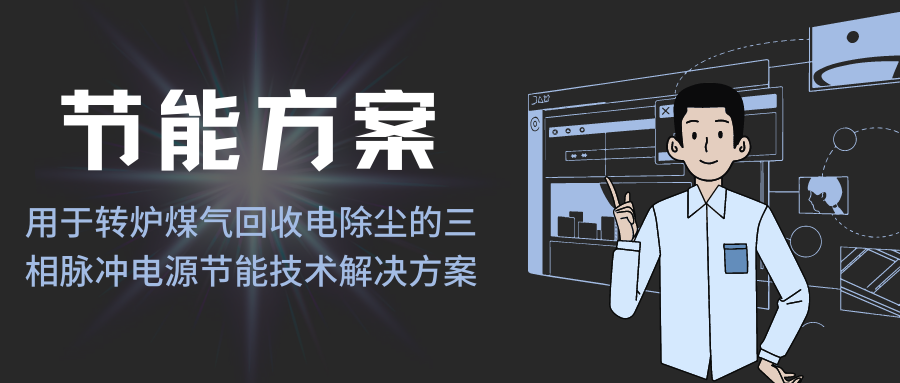
01
引言
干法转炉煤气回收电除尘技术是广泛应用于钢铁行业转炉炼钢煤气回收除尘技术,对于回收煤气质量起到至关重要的作用。转炉出口的粉尘浓度很高,在吹炼阶段的粉尘浓度最高可达200g/Nm³,因此高压电源的规格都要比其他工艺的除尘电源要大得多,一些大的转炉的除尘电源的规格甚至要超过2.5A/90kV,输入功率高达250kVA,一台除尘器需要有3~4台电源,能耗相当的高。
过去,转炉除尘器在做技改的时候,大都是从减排的角度优先考虑,但随着碳达峰、碳中和概念的提出与推广,如何在确保排放的前提下,进行节能减排,将会直接影响到业主的碳排放指标是否达标以及巨大的经济利益,因此业主的节能需求会越来越迫切。
本文将详细介绍传统转炉煤气除尘高压电源的技术现状、我司三相脉冲节能电源特有的脉冲功能、针对转炉煤气干式电除尘设计的深度节能方案以及现场应用的实际节能案例。
02
传统转炉煤气除尘高压电源的技术现状
转炉烟气中含有大量的金属成分,在除尘器的第一电场一般会因为低比电阻的粉尘导致阴阳极间的烟气介质被击穿而发生闪络放电,阻碍了电场电压的提升,于是荷电电压低于一电场闪络放电电压的粉尘都会被一电场所捕获,更高荷电电压的粉尘进入了第二电场。
在第二电场中,由于低比电阻的粉尘已经被捕获,烟气的击穿电压提升,于是二电场的电压、电流、能耗都要高于一电场,于是荷电电压低于二电场闪络电压的粉尘在二电场被捕获,后续电场的状况以此类推。
从一电场到末电场,粉尘越来越少,越来越难以荷电,对峰值电压的要求越来越高,击穿电压越来越高,实际运行的平均电压电流越来越高,因此能耗也越来越高。但其实后级电场粉尘含量很低,绝大部分的电能都被用于空气的荷电,能源的利用率很低。
目前,转炉行业使用的除尘电源除了我们的三相脉冲电源之外,其他电源厂家的都是非脉冲电源。
非脉冲电源的输出电压是平直连续的,峰值电压基本等于平均电压。在进行节能的时候,在降低平均电压和平均电流的同时,峰值电压也在下降,能够荷电的粉尘的数量在减少。这与能耗最高的、节能潜力最大的后级电场对于高峰值电压的需求是相矛盾的,即在节能的同时牺牲了粉尘的荷电能力。由于烟气中不同粒径、成分的粉尘荷电电压是不一样的,它们在数量上呈现出金字塔形的分布如下图所示。
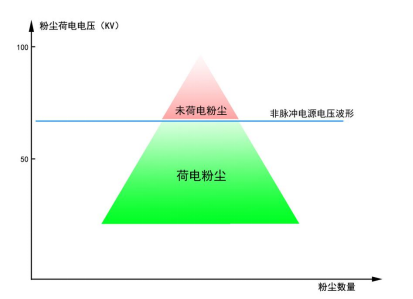
非脉冲电源电压波形与荷电粉尘数量的关系
电场力对未荷电的粉尘没有任何的吸附力,从上图可以看出,每下降一点电压都会导致大量的粉尘进入非荷电区,无法荷电,因此非脉冲电源在低浓度的烟气工况下不敢把平均电压平均电流降得太低,否则会影响前一级收不下来的粉尘的荷电,因此节能效果一般。
而且传统节能模式没有与转炉吹炼的控制设备建立通讯,无法感知目前的转炉正在进行的工艺流程,对于高浓度粉尘和低浓度粉尘都采用一样的电源输出设置,为了保证高粉尘浓度工艺流程阶段的出口排放,牺牲了低粉尘浓度工艺流程阶段的能耗。
03
三相脉冲节能电源的节能技术
三相脉冲节能电源是我司第二代的三相除尘高压电源,也是目前国内唯一具有脉冲功能的三相除尘高压电源。
经过十几年的持续改进和技术沉淀,该电源具有可靠性高、除尘效率高、节能效果明显,复杂烟气工况适应性好等优点。
在钢铁、电力、有色、水泥等行业广泛应用,并已取得十几个干式除尘器出口排放低于10mg/Nm³的工程业绩。
针对传统非脉冲电源的技术弊端,我们为转炉煤气回收电除尘设计了两套节能方案,可根据业主设备的实际情况进行选择,从而实现不同程度的节能效果。
方案一
非现场感知模式
目前业内转炉煤气电除尘均采用该模式,在这个模式下,我司方案的与众不同之处在于三相脉冲节能电源既能与传统电源一样连续输出平直的高压,又具有脉冲输出方式,而传统电源只能工作在连续输出模式下。
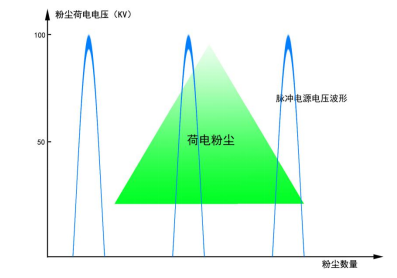
脉冲电源电压波形与荷电粉尘数量的关系
电除尘高压电源有两个重要的技术参数,峰值电压和平均电压。
峰值电压决定了粉尘能不能荷电,电场力对未荷电的粉尘没有任何的吸附力;
平均电压决定了荷电粉尘向极板运动的驱进速度,除尘器的长度有限,如果平均电压太低,荷电粉尘有可能还未运动到极板就会被烟气带出除尘器。
我们的脉冲电源每个脉冲送出的都是额定峰值电压,通过调节脉冲输出频率来控制输出的平均电压平均电流,保证粉尘有一定的驱进速度。
这样就可以在实现节能的情况下不降低对高比电阻粉尘的荷电能力,也就不会在大幅节能的情况,大幅降低除尘效率(如上图所示)。
通过脉冲方式,可以在无法与吹炼控制系统通讯的情况下,在高能耗低粉尘浓度的后级电场,送出峰值电压高达100kV的高能量脉冲,同时降低脉冲的输出频率,相比传统电源,即保证了除尘效率,又能节约大量的能源。
方案二
现场感知模式
转炉炼钢时,一炉钢水的冶炼时间大致在30分钟左右。
要经过兑废钢、兑铁、吹炼、补吹、出钢、溅渣、出渣这七道工艺,一炉钢水才算冶炼完成。
在这七道工艺中,以吹炼和补吹这两道工艺的粉尘浓度最高,最高可达到100~200g/m³,而其他几道工艺,粉尘浓度则低得多,在几百毫克~几克每立方米之间。
很显然,当粉尘浓度不同的时候,需要除尘电源提供的能量也是不同的。
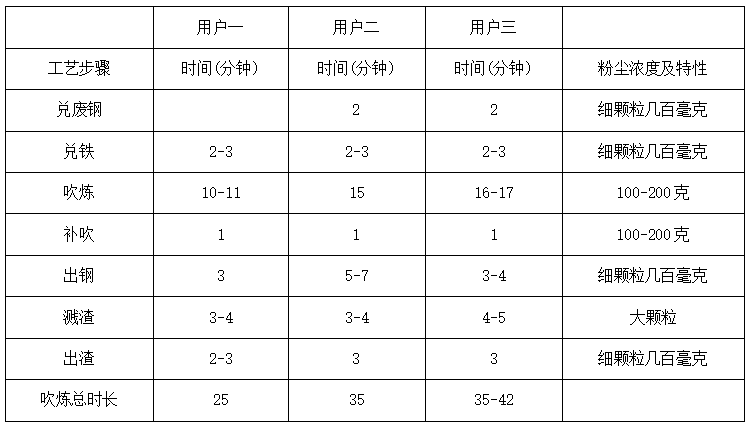
转炉各工艺流程的时长及粉尘浓度
我们从3家不同的钢厂获取他们的生产工艺数据。
如上表所示,列举了他们的转炉每个工艺流程所需的时间以及对应的粉尘浓度和特性。
通过与转炉吹炼控制设备建立通讯,除尘电源能够实时感知到转炉目前正在进行的工艺,获取到目前粉尘浓度的情况,高压电源可以通过调试阶段获得的基础运行参数,根据正在进行的工艺流程自动选择最佳的脉冲输出频率,在保证排放的情况下,取得最佳的节能效果。
吹炼和补吹这两个高粉尘浓度工艺阶段的持续时间,差不多占据一个转炉冶炼周期时长的一半左右,即低粉尘浓度工艺阶段也有一半的时长,大幅减少低粉尘浓度工艺阶段的能耗,对于除尘系统的节能有着非常重大的意义。
现场感知模式是非现场感知模式的延伸和扩展,能够更精细化地控制电源的能耗,能够比非现场感知模式,更进一步地大幅度节能。
04
三相脉冲电源的转炉节能案例
2020年3月,我们用使用三相脉冲电源对河北某钢厂进行了转炉电除尘器的电源节能改造。
该厂1#转炉除尘器配置的是我司的4台单相高压电源。
2#除尘器配置的是国内某公司的1台三相非脉冲电源+3台单相电源。
1#2#转炉的大小,生产工艺完全一致,两台除尘器的收尘面积,烟气流速等主要参数也基本一致。
由于2#炉的除尘器能耗一直比1#炉的要高,于是业主便选择我们的三相脉冲电源对2#炉的除尘器进行了一次节能改造。改造前后每吹练一吨钢水的除尘器电耗如下两表所示。
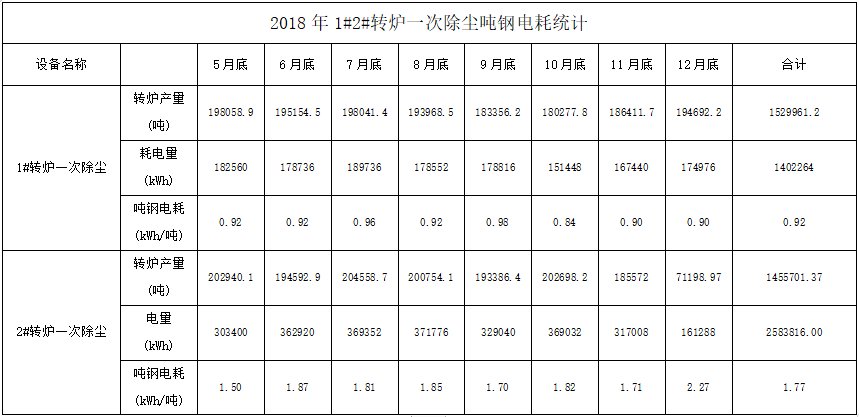
2018年1#2#除尘器吨钢电耗
2#炉在电源改造前,每吹炼一吨钢的除尘器电耗为1.7~1.8度之间,远高于我司单相电源的0.9度的电耗。
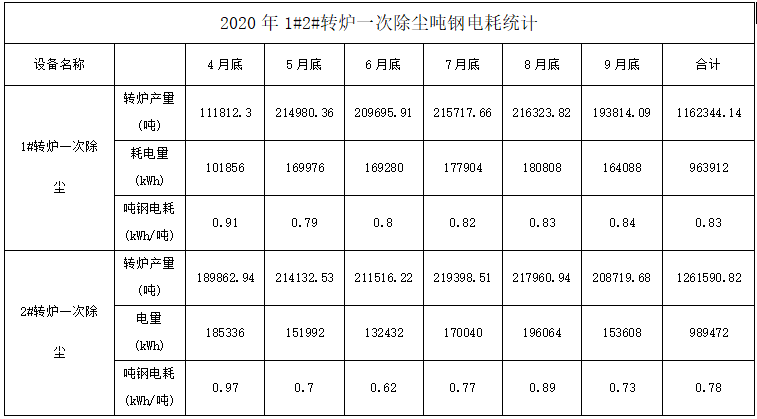
2020年改造后1#2#除尘器吨钢电耗
2020年2#炉在完成节能改造,更换成三相脉冲节能电源后,吨钢电耗降到了0.7~0.8度左右,节能达到50%。在确保排放的情况下,节能效果非常显著。
由于业主没有在改造后对烟囱排放进行检测,因此无法确定改造后的具体排放结果,但从高压的运行数据及烟囱口的目测结果,出口排放是比原电源系统更好的。
由于业主无法提供硬接点或通讯的方式,让高压电源与吹炼控制系统进行通讯,所以无法使用现场感知模式,因此无法进行深度节能,否则2#炉的能耗还将进一步地大幅降低。
虽然国家和环保机构很早就提出“节能减排”的口号,相关企业也进行了一些节能改造,但不少项目在节能方面还是做得比较粗放。
尤其是在转炉煤气回收除尘领域,业主过于关注排放而忽视了节能。由于这样的市场导向,导致了电源厂家对产品的节能并没有那么重视,也没有细致地去分析转炉煤气回收的工艺特点。
本文提供的两个节能方案可以很好地降低转炉电除尘吨钢的电耗,具有很强的推广价值,也有很好的借鉴意义。
目前国家正在大力倡导“碳中和”,势必会在许多行业引起新一轮的“节能减排”运动,三相脉冲电源特有的节能模式,必将在这一轮“节能减排”运动中做出自己应有的贡献。
扫码关注我们